Precision Injection Molding: The Future of Manufacturing
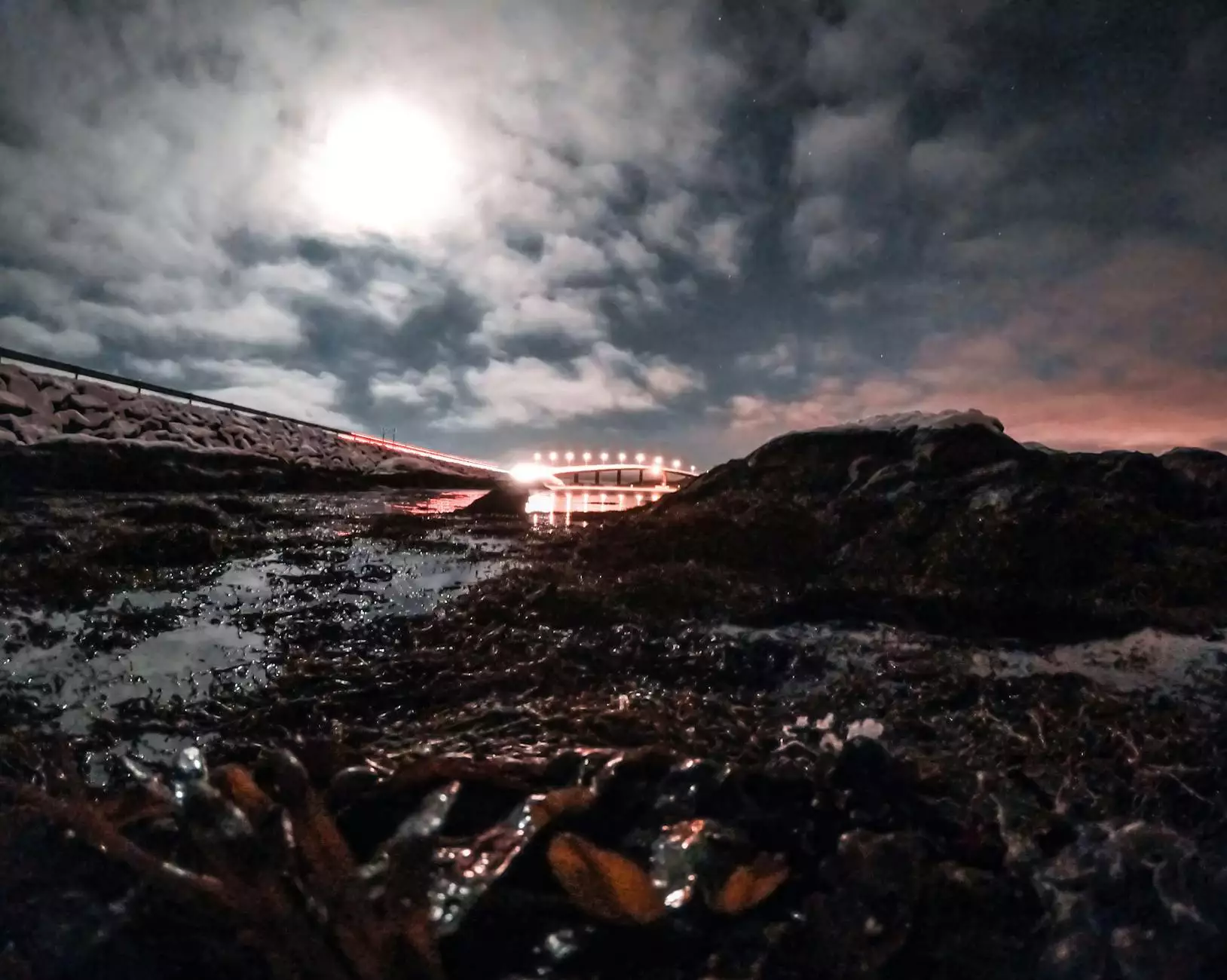
Precision injection molding is a transformative technique that has revolutionized the manufacturing landscape across various industries. This technology not only enhances product quality but also elevates efficiency, making it indispensable for modern manufacturing processes.
What is Precision Injection Molding?
Precision injection molding is a manufacturing process that involves injecting molten material (typically plastic) into a precisely engineered mold to produce highly accurate and repeatable parts. This method is essential for producing complex shapes with tight tolerances, making it a favorite among industries that demand high precision and reliability.
The Benefits of Precision Injection Molding
The adoption of precision injection molding in manufacturing comes with numerous benefits:
- High Precision: The process can produce parts with tolerances as tight as ±0.001 inches, which is crucial for applications in automotive, aerospace, and medical industries.
- Cost Efficiency: Although the initial setup costs can be high, the long-term savings through mass production and reduced material waste make it cost-effective.
- Complex Geometries: Precision injection molding can create intricate designs that are difficult, if not impossible, to achieve through traditional manufacturing methods.
- Material Versatility: It offers the flexibility to use a wide range of materials, including thermoplastics, thermosets, and elastomers.
- Consistency: Batch-to-batch quality is maintained, assuring uniformity across mass-produced items.
Applications of Precision Injection Molding
The applications of precision injection molding span multiple industries:
1. Automotive Industry
In the automotive sector, precision injection molding is used to produce components such as dashboards, panels, and various interior parts that require a perfect fit and finish. The ability to engineer parts with high precision enhances vehicle performance, aesthetics, and safety.
2. Medical Devices
The medical industry demands the highest standards in precision and hygiene. Precision injection molding allows for the production of instruments and components such as syringes, surgical instruments, and implantable devices, with meticulous attention to detail.
3. Consumer Goods
Everyday products, from electronics casings to kitchen gadgets, benefit from precision injection molding. The technology ensures that these products meet ergonomic standards and aesthetic values.
4. Aerospace
In aerospace, where safety and performance are paramount, precision injection molding helps create lightweight yet durable components that contribute to fuel efficiency and overall aircraft functionality.
How Precision Injection Molding Works
The precision injection molding process generally follows these steps:
- Material Selection: The first step involves selecting the appropriate material based on the application requirements.
- Mold Design: Engineers design a mold that meets precise specifications and tolerances required for the end product.
- Heating and Injection: The selected material is heated until it becomes molten and is then injected into the mold under high pressure.
- Cooling: Once the mold is filled, cooling channels remove heat from the material, allowing it to solidify and take the mold shape.
- Demolding: After cooling, the mold opens to release the part, which may require additional finishing processes before it is ready for use.
The Importance of Quality Control
In precision injection molding, quality control is critical. Manufacturers implement various inspection and testing methods to ensure that the parts produced meet the specified tolerances and quality standards. Some common quality control strategies include:
- Dimensional Inspection: Using tools like calipers and micrometers to measure the dimensions of molded parts.
- Visual Inspection: Checking for surface defects, blemishes, or inconsistencies in color and texture.
- Functional Testing: Conducting tests to ensure that the parts perform their intended functions under various conditions.
The Future of Precision Injection Molding
As technology advances, the future of precision injection molding looks promising. Innovations in materials, automation, and process management are set to enhance the capabilities of injection molding. Some key trends to watch include:
- Smart Manufacturing: Integration of IoT (Internet of Things) will allow real-time monitoring and data collection, improving efficiency and reducing downtime.
- Biodegradable Materials: Increasing demand for environmentally friendly alternatives is pushing the industry toward biodegradable and recyclable materials.
- 3D Printing Integration: The combination of 3D printing with injection molding processes can allow for rapid prototyping and reduced lead times.
Choosing the Right Injection Molding Partner
Selecting the right partner for precision injection molding can significantly impact the success of a project. Companies like DeepMould.net offer comprehensive services that can cater to various needs. When choosing a partner, consider the following:
- Experience: Look for a company that has significant experience in your industry.
- Technology: Assess the technology and processes they use to ensure they align with modern manufacturing standards.
- Quality Assurance: Check their quality assurance protocols to ensure they meet your quality requirements.
- Customer Service: Strong communication and support will aid in smooth project execution.
Conclusion
In conclusion, precision injection molding represents a vital component of modern manufacturing. Its ability to produce high-quality, complex parts consistently makes it a go-to choice for numerous applications across various sectors. As technology continues to evolve, so will the capabilities and applications of precision injection molding, promising exciting developments for manufacturers and consumers alike. For those in need of advanced molding solutions, seeking partners with expertise and a commitment to quality, like DeepMould.net, is essential for success in today's competitive landscape.