The Importance of Injection Mould Companies in Modern Manufacturing
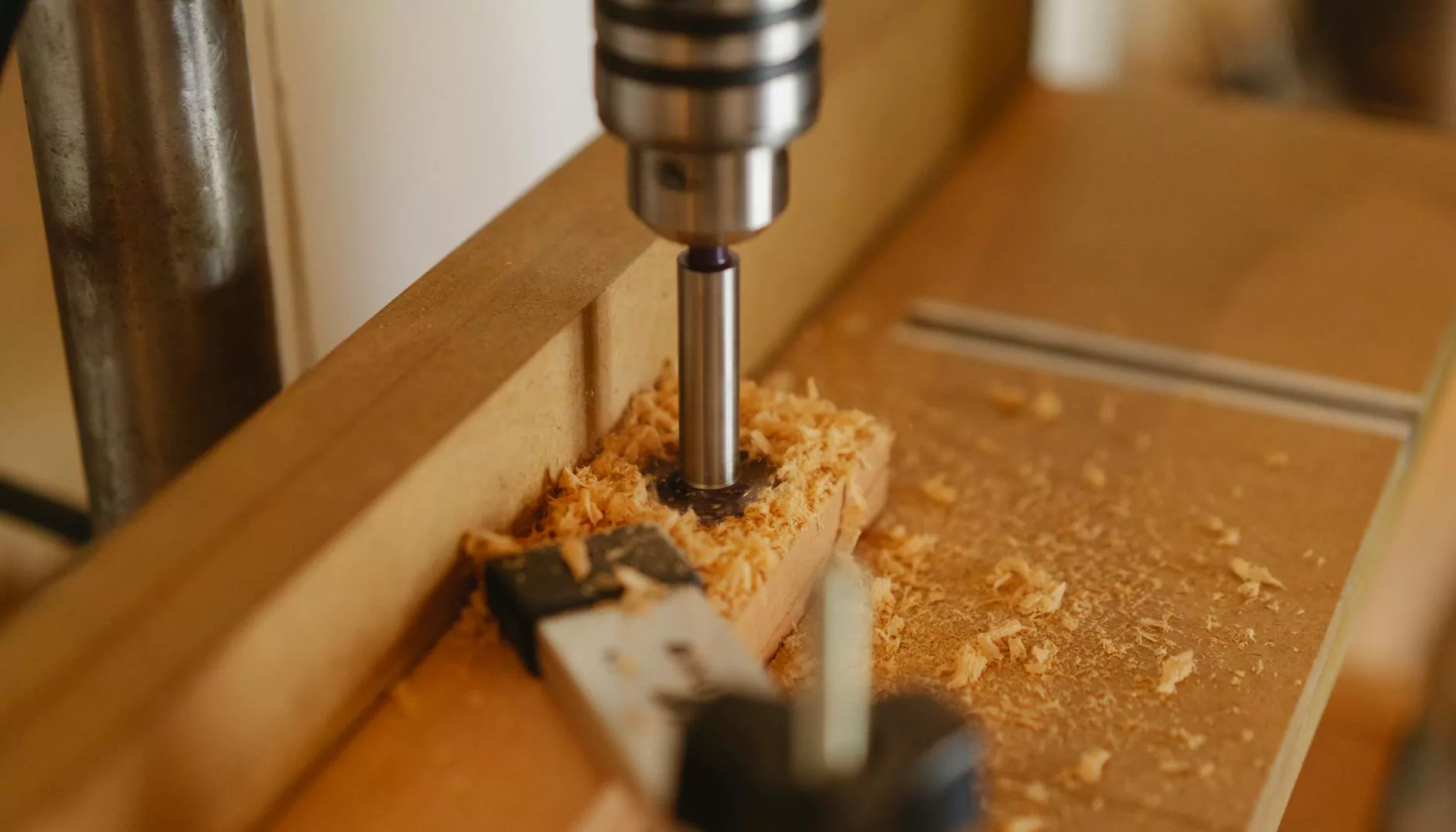
Injection mould companies play a pivotal role in the manufacturing landscape, providing crucial services that facilitate the mass production of high-quality products across various industries. As the demand for efficient, durable, and cost-effective production methods grows, these companies have become indispensable partners for businesses looking to innovate and thrive.
Understanding Injection Moulding: A Key Manufacturing Process
At its core, injection moulding is a manufacturing process used to produce parts by injecting molten material into a mould. This process is primarily used for manufacturing plastics but can also accommodate metals and other materials. The versatility and efficiency of injection moulding make it a popular choice for a wide array of products, from everyday household items to intricate components used in aerospace and automotive industries.
The Advantages of Working with Injection Mould Companies
Engaging with injection mould companies offers numerous advantages that can significantly impact production efficiency and product quality. Here are some key benefits:
- Cost-Effectiveness: Injection moulding is generally more cost-effective for large production runs due to the speed and efficiency of the process.
- High Precision: These companies utilize advanced technology that ensures high levels of precision and consistency in product manufacturing.
- Material Versatility: Injection moulding can work with a variety of materials, including thermoplastics, thermosetting plastics, metals, and more.
- Complex Shapes and Designs: Injection moulding allows for intricate designs that might be impossible with other manufacturing techniques.
- Reduced Waste: The process generates minimal waste compared to traditional manufacturing methods, making it more environmentally friendly.
How Injection Mould Companies Operate
The Process of Injection Moulding
The injection moulding process can be broken down into several key stages:
- Design: It all begins with the design of the part, where engineers and designers collaborate to create a 3D model that meets specifications.
- Mould Creation: Once a design is finalized, a mould is crafted, which will shape the final product. This can require extensive precision work to ensure compatibility with the design.
- Injection: The selected material is heated until it becomes molten and is then injected into the mould at high pressure.
- Cooling: The moulded part is allowed to cool and solidify, taking the shape of the mould.
- Demoulding: After cooling, the part is removed from the mould, ready for further processing or finishing.
- Finishing: Finally, additional processing such as trimming, painting, or assembly may be done to meet the required specifications.
Key Industries Utilizing Injection Moulding
Injection mould companies cater to a wide range of sectors, providing tailored solutions that address specific industry needs. Some of the key industries benefiting from injection moulding include:
- Automotive: Producing components like dashboards, bumpers, and interior trims.
- Aerospace: Manufacturing lightweight yet durable parts that ensure safety and performance.
- Consumer Electronics: Creating housings and intricate components for devices such as smartphones and laptops.
- Healthcare: Developing medical devices, diagnostic equipment, and packaging for pharmaceutical products.
- Packaging: Providing containers, caps, and closures that meet stringent safety and quality standards.
Choosing the Right Injection Mould Company
When selecting an injection mould company, businesses should consider several factors to ensure they partner with a reliable and capable provider:
- Experience and Expertise: Look for companies with a proven track record in your specific industry.
- Technology and Equipment: Ensure the company uses modern and well-maintained machinery capable of meeting your production requirements.
- Quality Assurance: Check for certifications and commitment to quality control throughout the manufacturing process.
- Customizability: The ideal company should be able to adapt its services to meet your unique design specifications and production needs.
- Scalability: Consider whether the company can handle increased production demands as your business grows.
Future Trends in Injection Moulding
The landscape of injection moulding is continuously evolving, driven by innovation and technological advancements. Some exciting trends that are shaping the future of this industry include:
- Automation and Robotics: The integration of automation in the injection moulding process can enhance efficiency, reduce human error, and lower operational costs.
- Sustainable Practices: More companies are adopting eco-friendly materials and practices to minimize environmental impact and respond to consumer demands for sustainable products.
- 3D Printing Integration: The combination of traditional injection moulding with 3D printing allows for rapid prototyping and a more agile manufacturing process.
- Smart Moulding Technology: The use of IoT sensors and smart technology can optimize the injection moulding process for better monitoring and maintenance.
- Material Innovations: Ongoing research in polymers and other materials leads to the development of stronger, lighter, and more sustainable options for moulding.
Conclusion
In summary, injection mould companies are essential to the efficient and effective production of a vast array of products in today's manufacturing ecosystem. Their ability to provide cost-effective, high-precision, and versatile manufacturing solutions makes them invaluable partners to businesses across multiple industries. As technology continues to advance, these companies will undoubtedly play a crucial role in shaping the future of manufacturing.
About DeepMould.net
For businesses seeking reliable partnerships in the realm of injection moulding, DeepMould.net stands as a leader among injection mould companies. With a commitment to quality, innovation, and customer satisfaction, DeepMould.net is equipped to handle all your moulding needs with expertise and efficiency.