The Comprehensive Guide to Hydraulic Flanges
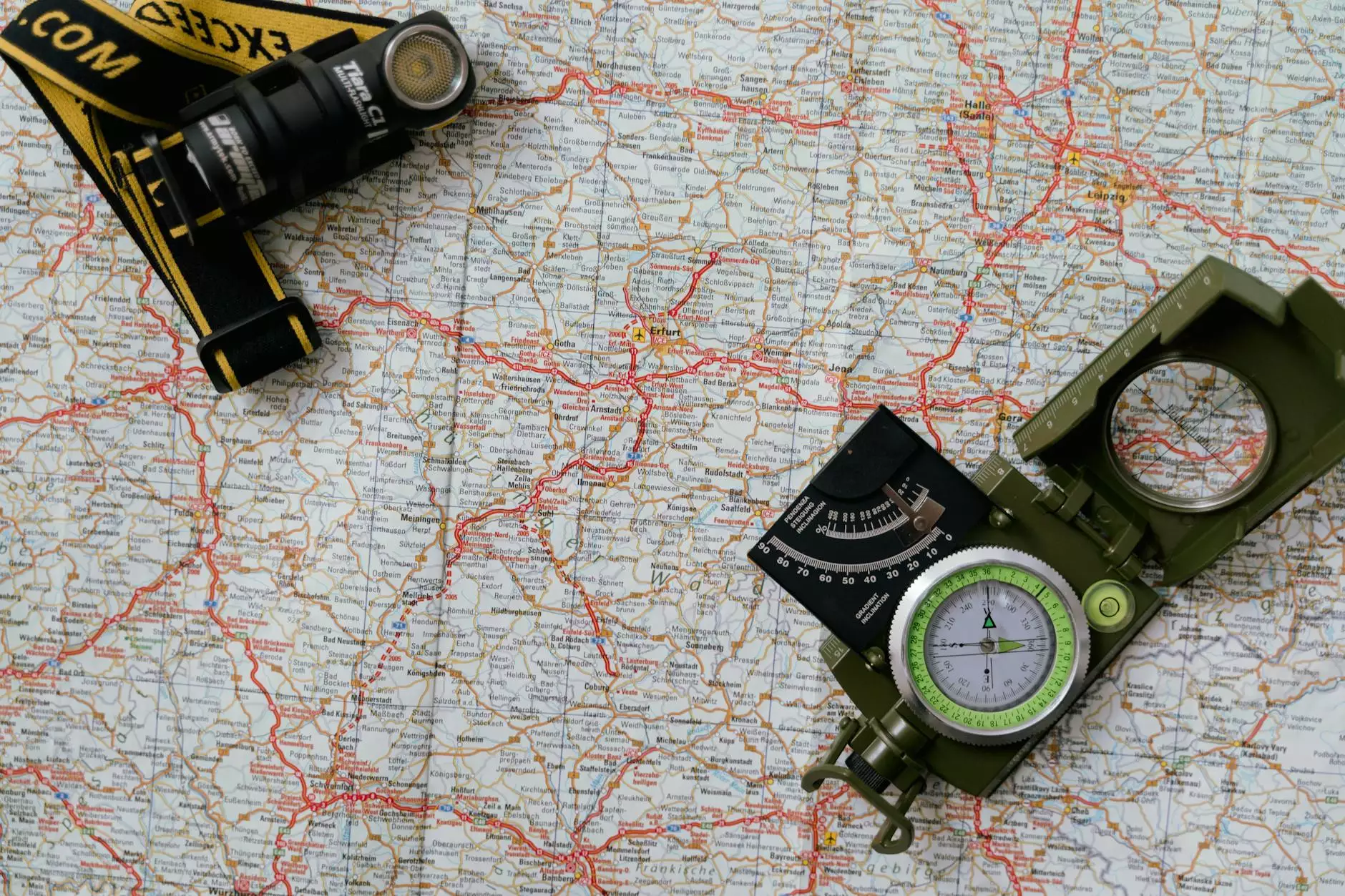
In the realm of industrial machinery and fluid systems, hydraulic flanges play a vital role in ensuring the integrity and efficiency of fluid transfer. This article aims to provide a thorough exploration of hydraulic flanges, covering their designs, applications, and the advantages they offer businesses that rely on hydraulic systems. Understanding these components can help you make informed decisions in your purchasing and application processes.
What are Hydraulic Flanges?
Hydraulic flanges are essential components used to connect hydraulic tubes and hoses. They provide a robust and reliable interface between pipes, ensuring a leak-proof connection that can withstand high pressures. Typically made from materials like steel, stainless steel, or aluminum, these flanges are engineered to endure the harsh conditions often found in industrial environments.
Types of Hydraulic Flanges
There are several types of hydraulic flanges, each designed for specific applications and pressure ratings. Understanding these types is crucial for selecting the right flange for your requirements. Below are the most common types:
- Flat Face Flanges: These flanges have a flat sealing surface, which allows for even distribution of pressure. They are ideal for applications where a tight seal is required.
- Raised Face Flanges: With a slightly raised surface, these flanges enhance the sealing capability. They are often used in high-pressure situations.
- Lap Joint Flanges: These flanges are designed to fit over the pipe, allowing for flexibility in alignment. They are commonly used in applications where maintenance is key.
- Blind Flanges: Used to close off ends of piping systems, blind flanges do not have a hole for a bolt. They are often used in testing and maintaining pipelines.
- Slip-On Flanges: Designed to slide over the end of a pipe, slip-on flanges are easy to install and are perfect for lower pressure applications.
Applications of Hydraulic Flanges
The applications of hydraulic flanges are vast and critical across various industries. Here are some notable applications:
- Aerospace: Hydraulic systems in aircraft rely heavily on flanges to connect different hydraulic components securely.
- Construction: Heavy machinery such as excavators and bulldozers utilize hydraulic flanges for their hydraulic systems to operate efficiently.
- Manufacturing: In factories where precise fluid control is essential, hydraulic flanges ensure that hydraulic circuits function without leaks.
- Automotive: Hydraulic flanges are integral in power steering systems and braking systems, providing reliable connections that enhance vehicle safety.
- Marine: Hydraulic systems in ships and boats also depend on durable flanges to ensure fluid transfer under varying temperatures and pressures.
The Importance of Quality in Hydraulic Flanges
Choosing high-quality hydraulic flanges is fundamental for maintaining the efficiency and safety of any hydraulic system. Here are some reasons why quality matters:
- Durability: High-quality flanges are designed to withstand extreme conditions, reducing the likelihood of wear and tear.
- Leak Prevention: Quality flanges provide superior sealing capability, which prevents hydraulic fluid leaks that can lead to costly downtime.
- Reduced Maintenance Costs: Investing in quality translates to lower maintenance requirements, allowing businesses to focus on their core operations.
- Compliance with Standards: Well-manufactured flanges adhere to industry standards, ensuring that they meet safety and performance regulations.
How to Choose the Right Hydraulic Flange
Selecting the right hydraulic flange requires careful consideration of several factors:
1. Application Environment
Assess whether the flange will be used in a high-temperature or corrosive environment. This will help you choose the right material.
2. Pressure Rating
Understand the pressure levels your system will be operating under to select a flange that can handle those pressures without risk of failure.
3. Size and Dimensions
It’s crucial to select a flange that matches the diameter and thickness of your pipes to ensure a proper fit.
4. Mounting Style
Consider whether a slip-on, blind, or lap joint style is appropriate for your installation needs.
Advantages of Hydraulic Flanges
Implementing hydraulic flanges into your systems provides numerous advantages, enhancing overall operational efficiency. Here are the key benefits:
- Enhanced Safety: By preventing leaks and maintaining structural integrity, hydraulic flanges contribute to a safer working environment.
- Versatility: Due to their variety in styles and materials, hydraulic flanges can be utilized in nearly any hydraulic application.
- Cost-Effectiveness: With lower maintenance needs and reduced risk of failure, flanges can save money in the long run.
- Improved Performance: The right flange can optimize fluid flow and system pressure, leading to better performance of hydraulic systems.
Conclusion
In conclusion, hydraulic flanges are indispensable components in a variety of industrial applications. Choosing the right flanges can significantly affect the performance, efficiency, and safety of hydraulic systems. For businesses in need of high-quality fittings, fitsch.cn offers a suite of fittings for sale, ensuring you have access to reliable and durable hydraulic solutions. By investing time in understanding these components, you position your business for greater efficiency and reduced operational costs.