Exploring Precision Injection Molding and Its Advantages in Metal Fabrication
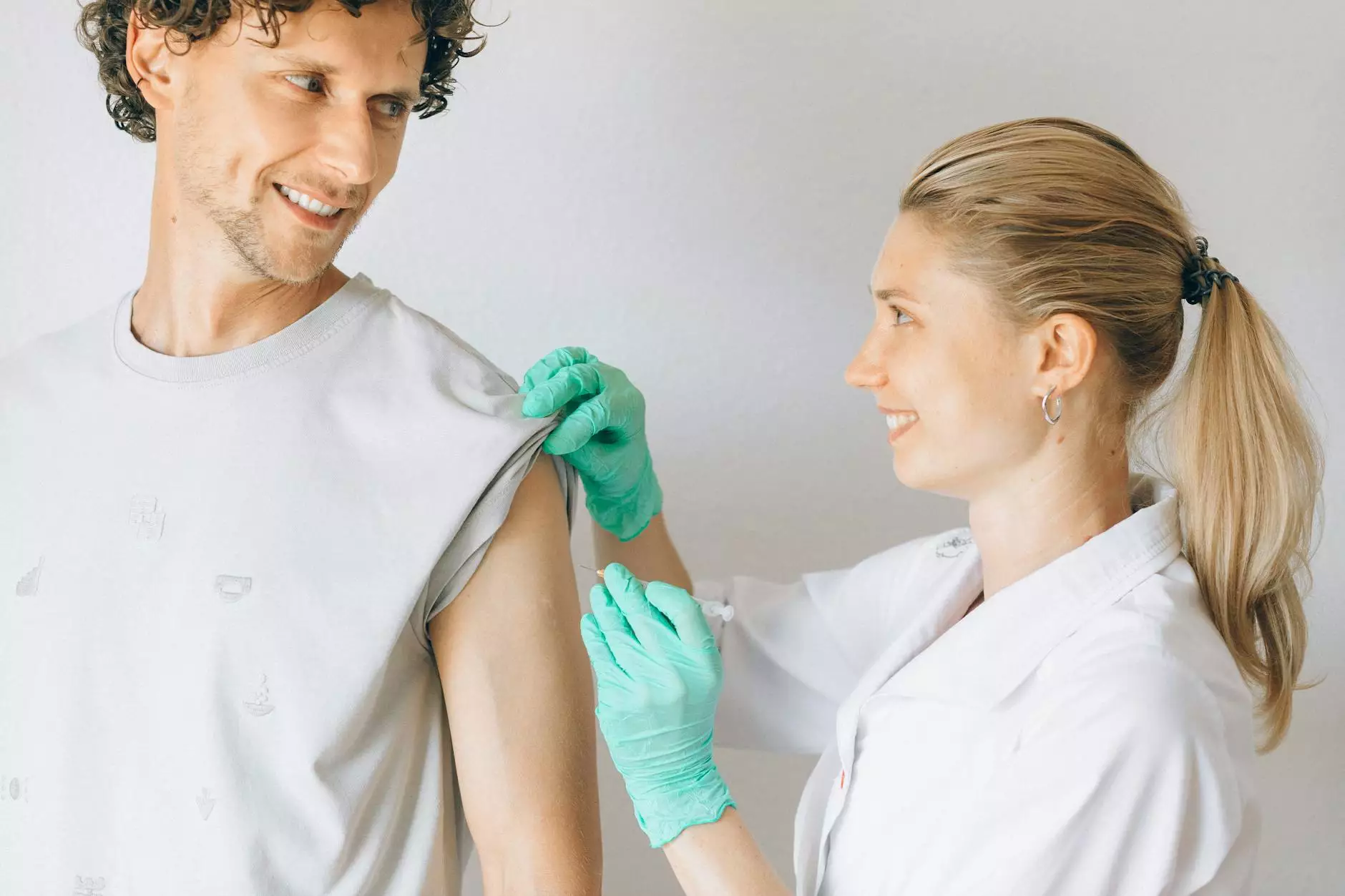
The manufacturing industry has seen remarkable advancements over the years, particularly in the field of precision injection molded components. This innovative process is transforming how products are designed, produced, and utilized across a myriad of sectors. At DeepMould.net, we delve into the myriad ways precision injection molding not only enhances productivity but also contributes to superior product quality in metal fabricators.
Understanding Precision Injection Molding
Precision injection molding is a manufacturing process that involves injecting molten materials into a mold to create specific, detailed components. While commonly associated with plastics, this technique has been adapted for metal fabrication as well. By using advanced technologies and high-quality materials, manufacturers can produce intricate designs that adhere to tight tolerances and consistent quality standards.
How Precision Injection Molding Works
The process of precision injection molding consists of several stages:
- Material Selection: The chosen material, whether plastic or metal, is critical for achieving the desired results.
- Mold Design: Designers create detailed molds that reflect the exact specifications required for the final product, incorporating features that allow for smooth injection and easy ejection.
- Injection Process: The molten material is injected into the mold under high pressure, filling every intricate detail of the cavity.
- Cooling and Solidification: Once the mold is filled, the material is allowed to cool and solidify, forming a rigid structure.
- Mold Removal: After cooling, the mold is opened, and the precision component is removed.
- Finishing Touches: Depending on the requirements, additional processes such as surface treatment, painting, or assembly may be applied.
The Advantages of Precision Injection Molding
Adopting precision injection molded components in metal fabrication presents numerous benefits. Here are some of the key advantages:
1. High Precision and Accuracy
Precision injection molding allows manufacturers to achieve high levels of accuracy in the dimensions and tolerances of their components. This is particularly important in industries where even the smallest deviation can lead to significant issues, such as in aerospace and medical devices.
2. Increased Efficiency
The automation of the injection molding process reduces manual labor and significantly speeds up production times. Manufacturers can produce large volumes of components in a short timeframe, leading to enhanced operational efficiency.
3. Cost-Effectiveness
Although the initial investment for molds can be high, the cost per part decreases with high-volume production. Furthermore, the reduced scrap rates and minimized need for post-processing contribute to cost savings in the long run.
4. Design Flexibility
Designers can create complex geometries and intricate features that would be impossible or prohibitively expensive to achieve with traditional manufacturing methods. This design flexibility enables innovation and customization of products.
5. Material Versatility
While traditionally used for plastics, advances in technology have allowed for precision injection molded metals, offering a wide range of materials including aluminum, steel, and alloys. This versatility opens up new applications for industries such as automotive and electronics.
Applications of Precision Injection Molding in Metal Fabrication
The applications of precision injection molded components are vast, impacting various industries:
1. Automotive Industry
In the automotive sector, precision injection molding is widely utilized for producing lightweight and durable parts that enhance vehicle performance and fuel efficiency. Components like engine brackets, transmission cases, and housings are often manufactured using this technique.
2. Aerospace Sector
The aerospace industry requires components to meet stringent regulations concerning safety, performance, and weight. Precision injection molded parts are ideal for creating complex assemblies that contribute to the high performance demanded in aircraft design.
3. Medical Devices
In the medical field, precision and cleanliness are paramount. Precision injection molding allows for the manufacturing of high-quality, sterile components such as surgical instruments and laboratory equipment, ensuring compliance with health standards.
4. Electronics Industry
Precision molded parts are extensively used in the electronics sector for creating housings, connectors, and various electronic components that require high tolerances and intricate designs.
Innovation and Future Trends
The future of precision injection molding is bright, with ongoing innovations driving the industry forward. Some key trends to watch include:
- Advanced Materials: Development of new materials that enhance the performance characteristics of molded components, including lightweight composites and high-strength alloys.
- Smart Manufacturing: The integration of IoT and AI with manufacturing processes to enhance efficiency, monitor quality, and facilitate predictive maintenance.
- Sustainability Initiatives: Focus on eco-friendly materials and processes that reduce waste and energy consumption while promoting recycling within production frameworks.
- 3D Printing Integration: Combining traditional injection molding with 3D printing technologies allows for rapid prototyping and testing, streamlining the design phase.
Conclusion
In the realm of metal fabrication, precision injection molded components are revolutionizing manufacturing practices, driving efficiency, reducing costs, and enhancing product quality. As we embrace new technologies and innovations, industries ranging from automotive to aerospace will continue to harness the power of precision molding to meet the ever-evolving demands of the market.
For businesses like DeepMould.net, adopting precision injection molding is not just a choice; it is an investment in the future of manufacturing, innovation, and excellence. As the landscape of production continues to evolve, staying ahead through advanced techniques and practices will be crucial for success.